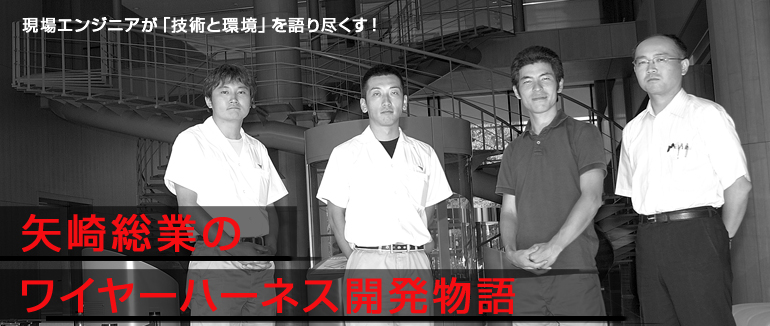
自動車用ワイヤーハーネスの大手サプライヤーとして、全世界市場でシェアトップクラスを誇る矢崎総業(以下、矢崎)。電子制御機構のネットワークをつかさどり、「クルマの神経」といわれるワイヤーハーネスは近年で大幅に進歩。同社は、電線の細線化(最も細いものは0.13平方ミリメートル!)や回路の高効率化、コネクタの軽量化と耐久性アップ、車両ネットワークの再編成などを達成し、世界中の完成車メーカーから大きな信頼を獲得している。
ここで1つの疑問が湧き起こる。なぜ矢崎は、世界中のクルマ開発のプロをうならせるワイヤーハーネスを作り出すことができるのか。開発現場でらつ腕を振るう4人のエンジニアに、矢崎のワイヤーハーネス開発の現場について聞いた。
ワイヤーハーネスに関する主要部品を自社内で開発・製造
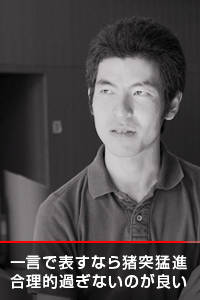
神戸 真 氏
自動車機器技術開発室
材料開発センター
第一材料開発部
2001年に新卒で入社。矢崎製品の材料開発を担う現在の部署で、ワイヤーハーネスに使われる電線の被覆材の開発を担当する。静岡県裾野のY-CITYに家族4人で暮らす
まずは、皆さんの仕事内容から教えてください。
加藤氏:私はトラックに組み込むワイヤーハーネスの開発設計を担当しています。国内外の完成車メーカーの技術者とやりとりしながらの仕事ですので、設計自体はもちろん、顧客側とのコミュニケーションにも気を使っています。
宮川氏:私は光通信用のワイヤーハーネスをつなぐコネクタの開発設計に従事しています。たくさんの情報を高速で処理する光通信が車両ネットワークとして使われるようになったのは、ここ最近。今は欧州の完成車メーカーが主な仕事相手です。
西原氏:私はいわゆる転職組で、以前の会社ではラジエーターなどに使うゴムホースの開発を担当していました。2006年に矢崎に入社してからは、材料開発センターでコネクタに使用する樹脂材の開発を行っています。
神戸氏:私は電線の被覆材の材料開発を手掛けています。メインの素材はオレフィン系。プラスチック材の中では比重が軽く、軽量化などに効果があるのですが、一方で硬いという特徴を持っています。これをより扱いやすくするのが、私の今の仕事です。
皆さんそれぞれ、ワイヤーハーネスに関するさまざまなパーツに携わっているんですね。
加藤氏:そう。そこが矢崎の大きな特徴で、電線、コネクタ、プロテクター、ジャンクションブロック、テープ、コルゲートチューブ、電子部品、メーターなど、ワイヤーハーネスにかかわる主要部品をすべて自社内で設計、開発、製造しています。そうすると……。
ワイヤーハーネスの仕組み全体が細かく理解できる。
加藤氏:その通り。そうするとワイヤーハーネス全体を考えながら、各パーツ開発ができ、結果的にはトータルでの品質管理や製品自体の進化につながるわけです。
今の加藤さんの発言に全員うなずいていらっしゃいますね。
宮川氏:トータルで品質管理ができると、トラブルへのリアクションも早くなりますよ。ここが問題だから、品質管理部と共同で解決しようとか。生産現場の方と相談することもありますよね?
神戸氏:ありますね、ちょっと怖い方もいらっしゃいますが(笑)。迷ったときに相談できる人は多いですよ。あと、ワイヤーハーネス全体の情報の共有もしっかりしています。
西原氏:確かに。製品開発の連続性を感じられるって良いですね。「自分が開発した材料が、ワイヤーハーネスのどこに使われ、どんな効果をもたらすか」が分かっているだけで、目の前の仕事の目的がつかめますから。
ワイヤーハーネス開発部門の合言葉は、「現場が原点」
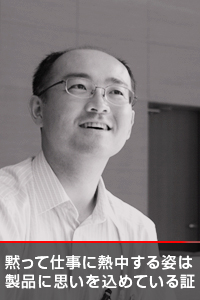
加藤孝幸 氏
自動車機器技術開発室
開発センター
第二開発設計部
工学博士
1994年に新卒で入社し、材料開発センターに配属。6年ほど長崎の大学共同研究員として派遣され、粉黛の研究に従事し、工学博士号を取得する。2005年より現職
現在の仕事内容に関して、やりがいや面白さって何ですか?
西原氏:私の場合は樹脂材の奥深さを知ったことでしょうか。コネクタの小型化、軽量化などで、樹脂材が担う役割は本当に大きい。あと、成型の加工時間短縮や生産性の向上なども重要な課題となってきます。苦労も多いですが、やりがいがありますよ。
宮川氏:私は自分が開発した光コネクタがきちんと機能して、生産現場やお客さまに納得してもらえた時に、この仕事の面白さを感じますね。あと、光通信は今後の車両ネットワークの発展に欠かせないものですから、その先端分野に携わっていることもやりがいです。
神戸氏:私のやっている被覆材の材料開発は、例えばパンを作る工程と同じだと思っています。水、粉、塩、砂糖などをどのように配合しておいしいパンを作るか。被膜材という組成物を仕上げるのにも、さまざまな素材の配合を自分の加減で作るわけです。このプロセスで試行錯誤するのが、本当に面白い。
加藤氏:ウマいたとえですね(笑)。私の場合は、現代のクルマで重視されている環境や安全などの面で、ワイヤーハーネスはどう貢献できるかを考え、実現したときにやりがいを感じますね。完成車メーカーの現場エンジニアから、「これは組み付けやすい」とか「軽くなったね」とか言われるとうれしいですよ。
神戸氏:今の加藤さんの話には、矢崎の開発現場の特徴が表れていると思います。つまり「現場が原点」ということ。ここでいう現場とは、ユーザー(完成車メーカー)の現場はもちろん、自社のワイヤーハーネスの生産現場も含まれます。
今の意見にまた皆さんうなずきましたね。
西原氏:「現場が原点」という考えは、私の部署内にも浸透しています。おそらく、ほかの部署でも同じじゃないですか?
加藤氏:分かりやすい例を挙げましょう。当社ではワイヤーハーネスの軽量化を重視していますが、実はこの目的の中には環境対策などのほかに、現場からの意見も含まれているんです。完成車メーカーの生産ラインでワイヤーハーネスを組み付ける箇所では、腱鞘炎や腰痛に悩んでいる人がいるという話を聞きます。少しでも軽くて組み付けやすいワイヤーハーネスを作って、生産現場で働く人の体への負担を軽減させたい―。こうした考えは、現場が原点だからこそ生まれる発想だと思います。
宮川氏:現場から出た意見は、ワイヤーハーネスに携わる開発部門全体でも情報共有されます。こうしたデータの蓄積は、非常に豊富ですよ。
【宮川氏が作っているのはコレ!】 光通信用コネクタ 新しい車両ネットワークとして注目を集める製品。「国内にはまだまだ普及していない分野なので、さらなる改良やコストの削減に挑んでいきたいです」 |
【加藤氏が作っているのはコレ!】 トラックなど大型車の軽量化、リサイクル性の向上、環境負荷の低減を目指し開発が進む。「矢崎の主力製品ですから、まだまだ進化させたいですね」 |
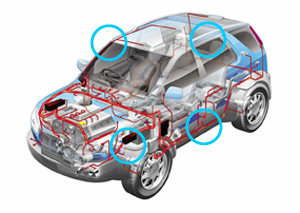
【西原氏が作っているのはコレ!】 コネクタ用の樹脂材料 コネクタの小型・軽量化、そして生産効率の向上を達成するためには、樹脂材の進化が必要不可欠。「生産効率の向上も課題の1つです」 |
【神戸氏が作っているのはコレ!】 プラスチックの中でも低比重のオレフィン系樹脂を扱う。「まだまだ発展途上の材料なので、さらなる性能向上に取り組んでいきたいですね」 |